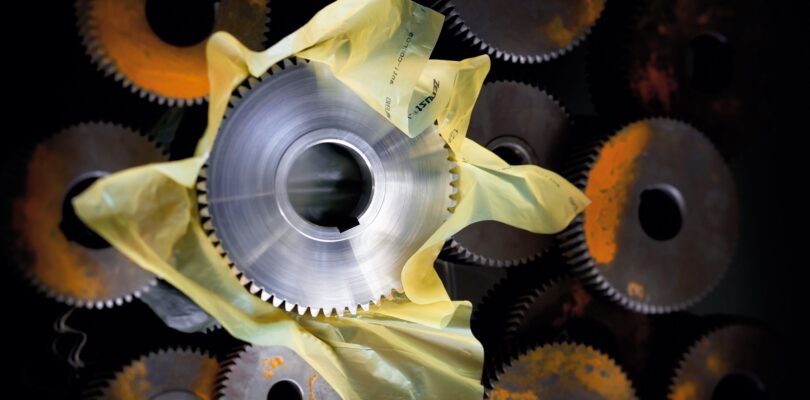
Moi klienci często zadają mi pytanie – dlaczego komponenty, które według nich są odpowiednio zabezpieczone i tak korodują? Wbrew pozorom, takie sytuacje w firmach produkcyjnych są dość powszechnym zjawiskiem. W najgorszym przypadku problem ten skutkować będzie koniecznością pokrycia dodatkowych kosztów związanych z obsługą reklamacji złożonej przez klienta. Wówczas zostaje narażona nasza relacja z klientem, w szczególności, gdy sytuacja się powtarza. Możemy jednak się przed tym uchronić gdy problem zostanie wykryty w ramach wewnętrznych procedur, przed ostateczną wysyłką zamówienia do klienta.
Niestety, przyczyny problemu zazwyczaj znajdują się po stronie producenta komponentów, który odpowiada za właściwe przygotowanie towaru do wysyłki. Ponadto możemy wskazać najczęściej występujące i powtarzające się błędy w procesie. Poniżej krótkie zestawienie czynników, które powodują korozję w Twoim zakładzie i jak sobie z nimi radzić.
Dbaj o czystość kąpieli i płynów technologicznych
W ramach procesu produkcyjnego używany jest szereg środków chemicznych – chłodziwa, oleje do obróbki metali, substancje smarne, płyny myjące i odtłuszczające lub inne kąpiele i płyny technologiczne, takie jak np. płyny używane przy wykonywaniu testów szczelności. Wszystkie środki chemiczne powinny być regularnie sprawdzane pod kątem zanieczyszczeń, jak i spełniania norm jakościowych. Niestety przez wielu ta czynność jest pomijana lub marginalizowana, a pozostawienie na powierzchni detalu zanieczyszczeń przyczynia się do przyspieszenia procesu korozji. Wśród wszystkich przypadków korozji w przemyśle automotive, aż 80% spowodowanych jest złym zarządzaniem gospodarką płynami w przedsiębiorstwie i brakiem kontroli parametrów kąpieli.
Stan jakości płynów, w tym stopień ich zanieczyszczenia można badać na wiele sposobów. Warto skonsultować tę kwestię z producentem środka chemicznego i zapytać o preferowane metody badawcze. Poniżej postaram się przybliżyć kilka z nich.
Skala pH
Metale żelazne stają się podatne na korozję przy pH mniejszym niż 9. Płyny do obróbki metali pracują w zakresie pH 8 – 10, natomiast alkaliczne środki myjące przy pH 7 – 10. Pomiar pH można prowadzić za pomocą papierków lakmusowych, co wiąże się z bardzo niską efektywnością pomiaru, za pomocą aparatury laboratoryjnej (pHmetr) lub za pomocą analizy ilościowej (miareczkowanie).
Suma rozpuszczonych ciał stałych TDS Total Dissolved Solids
Przewodność elektrolityczna wody zależy od sumy rozpuszczonych w niej jonów. To one przewodzą ładunek elektryczny. Jest to również wskaźnik zanieczyszczeń rozpuszczonych w cieczy – im wyższe, tym wyższa przewodność. Wyższa przewodność roztworu akceleruje korozję elektrochemiczną. Przewodność można badać za pomocą prostych przyrządów nazwanych konduktometrami. Nie jest to metoda najbardziej efektywna, dlatego proponowałbym użycie jej, jako metody wspomagającej ocenę stopnia zanieczyszczenia kąpieli.
Współczynnik refrakcji
Metoda badania załamania światła na próbce cieczy pobranej z kąpieli, za pomocą której możemy badać np. stężenie dodatku antykorozyjnego w roztworze. Niestety jest to metoda nieprecyzyjna, szczególnie w mocno zanieczyszczonych kąpielach wskazuje zafałszowane wyniki. Pomiar wykonuje się przy użyciu prostych urządzeń, np. refraktometru Brix’a.
Iron chip test
Najczęściej stosowaną przeze mnie metodą oznaczania stopnia zanieczyszczenia próbek płynów pobranych od klienta. Jest metoda Iron Chip Tests. Jest na tyle skuteczna, że przedstawia w bardzo jednoznaczny i dokładny sposób, czy testowany płyn może mieć wpływ na korozję detalu, czy też nie.
Badanie przeprowadza się zgodnie z normą ASTM D4627 Standard Test Method for Iron Chip Corrosion for Water–Miscible Metalworking Fluids. Odpowiednią dawkę wiórów żeliwnych (ok. 3 gram) umieszcza się na sączku, po czym w ten sposób przygotowaną próbkę metalu zalewa się próbką płynu pobranego z kąpieli (ok. 2 ml). Następnie wióry się usuwa i bada się stopień zanieczyszczenia sączka. Jeżeli żeliwo skorodowało, to ślady korozji pozostaną na sączku. To, w jakim stopniu będą one widoczne, pokaże nam jak bardzo zanieczyszczona jest nasza kąpiel. Poniżej dla porównania zdjęcia pokazujące jak wyglądał test dla płynu czystego i zanieczyszczonego
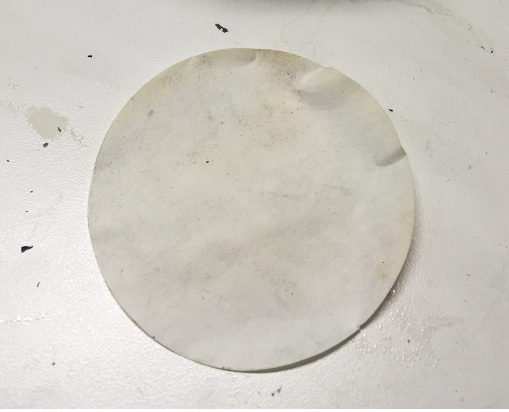
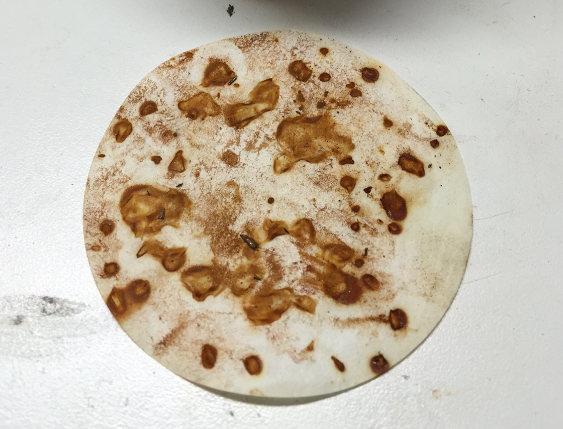
Warto podkreślić znaczenie dbałości o jakość kąpieli myjących, które w znacznym stopniu wpłynie na jakość produkowanych detali, co z pewnością przyczyni się do zmniejszenia ilości reklamacji z tytułu korozji dostarczonych komponentów.
Noś rękawiczki
Kolejną bardzo częstą przyczyną występowania ognisk korozji na elementach stalowych jest brak wewnętrznych przepisów dotyczących noszenia rękawiczek przez pracowników produkcyjnych. W skład potu ludzkiego wchodzi: woda, sól, tłuszcze oraz inne związki chemiczne, a jego pH zawiera się w przedziale 4,5 – 6, czyli jest czynnikiem powodującym korozję metali żelaznych. Szczęśliwie, jest to jeden z najprostszych do zidentyfikowania czynników korozjogennych, ze względu na rodzaj i charakterystyczny kształt ognisk korozji.
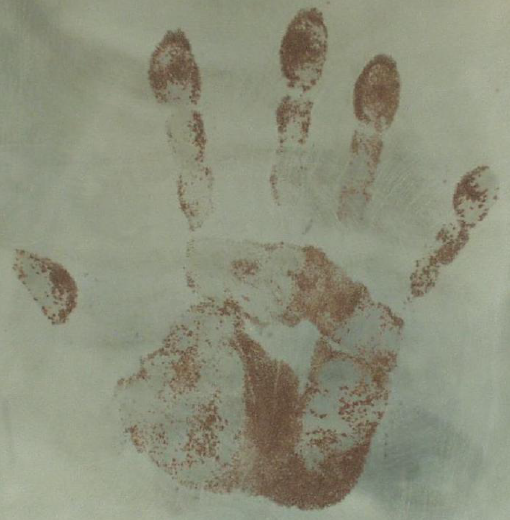
Nie narażaj komponentów na duże amplitudy temperatur
Dla lepszego omówienia następnej przyczyny, sprawdźmy sobie dwie skrajne sytuacje:
- Na zewnątrz jest 30 stopni, a Ty wyciągasz z lodówki zimny napój;
- Idziesz do sklepu po pieczywo. Okazuje się, że czeka na ciebie jeszcze ciepłe, ledwo wyjęte z pieca. Niestety ląduje w plastikowej torebce foliowej.
W obu powyższych przypadkach dojdzie do kondensacji pary wodnej. Problem ten dotyczy również komponentów pakowanych i składowanych w opakowaniach antykorozyjnych VCI, chociaż tylko na początku etapu pakowania. Jeżeli dojdzie do wykroplenia pary wodnej, zanim inhibitory korozji zaczną działać, opakowanie stanie się nieskuteczne. Do takich sytuacji dochodzi gdy np. umieszczamy ciepłe komponenty prosto po procesie obróbki metalu (np. po śrutowaniu) bezpośrednio do opakowania, lub gdy detale z ciepłego pomieszczenia przewożone są do pomieszczenia o niższej temperaturze (np. nieogrzewany magazyn). Należy mieć na uwadze, że w przypadku opakowań antykorozyjnych VCI, takie zjawisko może być niebezpieczne tylko na wczesnym etapie, gdy inhibitory korozji nie są jeszcze w stanie ochronić umieszczonych w nich detali. W momencie ustalenia się równowagi stężenia inhibitorów wewnątrz opakowania, komponenty zyskują pełną ochronę, nawet przy bardzo często zmieniających się temperaturach. W zależności od objętości, może to potrwać od kilkunastu minut do kilku godzin.
Nie dopuść do kontaktu kartonu z detalem
Wielu inżynierów odpowiedzialnych za projekt opakowania stosuje przekładki wykonane z kartonu jako element odgradzający warstwy detali w opakowaniu. Nie można zapominać, że karton jest materiałem organicznym i ma bardzo duże właściwości higroskopijne. Najczęściej detale umieszczone bezpośrednio na przekładce kartonowej wyglądają w ten oto sposób:
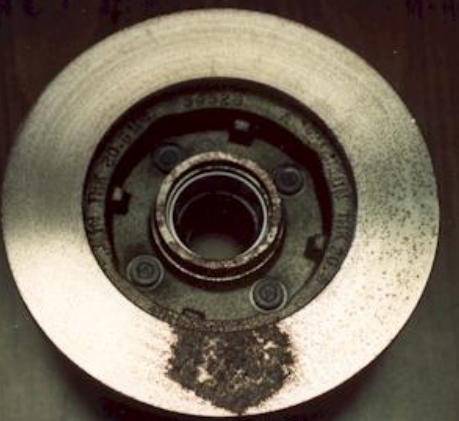
Aby w pełni wyeliminować to zjawisko, należy zastosować dodatkowy materiał izolujący powierzchnię metalu od przekładki (bardzo dobrze w tym przypadku sprawdza się papier antykorozyjny), lub wykorzystać do tego celu przekładki z tworzywa sztucznego, np. wykonane z polipropylenu arkusze płyty kanalikowej.
Zadbaj o dobór odpowiednich środków antykorozyjnych
Jeżeli decydujemy się na dobór odpowiedniego środka antykorozyjnego we własnym zakresie, warto swój wybór skonsultować z inżynierem odpowiedzialnym za produkt. Często w mojej praktyce ma miejsce sytuacja, w której klient dokonuje wyboru na podstawie danych marketingowych zaczerpniętych z internetu lub stron producenta. Warto mimo wszystko zrzucić brzemię odpowiedzialności i dać się wykazać osobie, która posiada odpowiednią wiedzę techniczną o danym procesie i będzie chciała się nią z nami podzielić.
Czasami wypadki przy pracy się zdarzają
Nawet przy najlepiej zabezpieczonym pakunku, może dojść do zdarzenia losowego lub błędu popełnionego przez osoby trzecie, w wyniku których transport może dotrzeć w innym stanie, niż byśmy tego oczekiwali. W jaki sposób można się przed tym uchronić?
- Dodatkowe wyposażenie ładunku we wskaźniki wstrząsu lub przechyłu, pozwolą zidentyfikować nieprawidłowości w transporcie towaru;
- Wyposażenie ładunku we wskaźniki wilgotności pozwoli nam określić, czy np. w trakcie rozładunku nie doszło do uszkodzenia, rozszczelnienia lub zalania ładunku;
- W skrajnych przypadkach można zaopatrzyć ładunek w specjalny datalogger, mierzący zmianę temperatury oraz wilgotności w czasie.
Konkluzja
Pamiętajcie, że 80% przypadków korozji spowodowane jest złą gospodarką płynów w procesie obróbki metali. Pozostałe 20% wynika z prostych do zidentyfikowania i wyeliminowania błędów ludzkich. Chętnie odpowiem na wszystkie pytania związane z Twoim procesem produkcyjnym. Można się ze mną skontaktować pod adresem e-mailowym: maciej.bloch@excor.pl.
Powiązane artykuły: